Budowa maszyn oraz ich projektowanie to procesy, które wymagają staranności i precyzji na każdym etapie. Pierwszym krokiem w tym skomplikowanym procesie jest analiza potrzeb i wymagań klienta, co pozwala na zrozumienie, jakie funkcje maszyna ma spełniać. Następnie przechodzi się do fazy koncepcyjnej, gdzie inżynierowie opracowują wstępne szkice oraz modele 3D, które pomagają wizualizować przyszły produkt. W tej fazie ważne jest również uwzględnienie aspektów ergonomicznych oraz bezpieczeństwa użytkowników. Kolejnym krokiem jest dobór odpowiednich materiałów, które będą użyte do produkcji maszyny. Wybór ten ma kluczowe znaczenie dla trwałości oraz efektywności działania urządzenia. Po zakończeniu etapu projektowania następuje faza prototypowania, gdzie tworzony jest pierwszy model maszyny. Prototyp jest testowany pod kątem wydajności oraz funkcjonalności, co pozwala na wprowadzenie ewentualnych poprawek przed rozpoczęciem masowej produkcji.
Jakie technologie są wykorzystywane w projektowaniu maszyn
W dzisiejszych czasach projektowanie maszyn opiera się na zaawansowanych technologiach, które znacznie ułatwiają i przyspieszają cały proces. Jedną z najważniejszych technologii jest komputerowe wspomaganie projektowania (CAD), które umożliwia inżynierom tworzenie szczegółowych modeli 3D oraz rysunków technicznych. Dzięki CAD możliwe jest również przeprowadzanie symulacji działania maszyny w różnych warunkach, co pozwala na wcześniejsze wykrywanie potencjalnych problemów. Kolejną istotną technologią jest analiza elementów skończonych (FEA), która pozwala na ocenę wytrzymałości konstrukcji i przewidywanie zachowań materiałów pod wpływem różnych obciążeń. Wykorzystanie druku 3D w prototypowaniu maszyn staje się coraz bardziej popularne, ponieważ umożliwia szybkie i tanie tworzenie modeli testowych. Dodatkowo, technologie takie jak Internet Rzeczy (IoT) pozwalają na monitorowanie pracy maszyn w czasie rzeczywistym, co zwiększa efektywność ich eksploatacji oraz ułatwia diagnostykę ewentualnych usterek.
Jakie są najważniejsze aspekty ergonomiczne w budowie maszyn
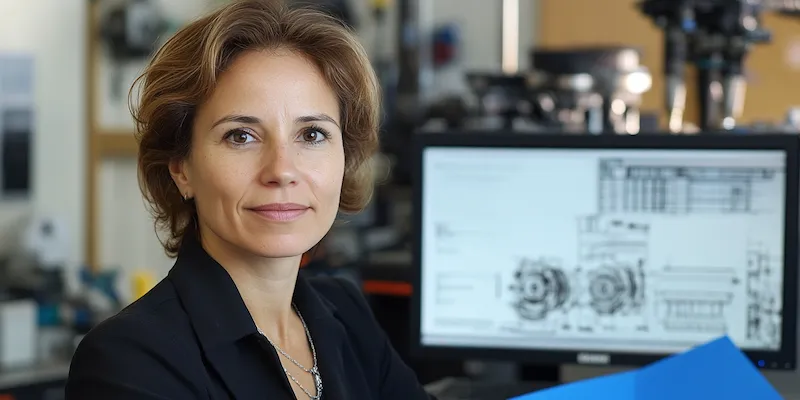
Ergonomia odgrywa kluczową rolę w budowie maszyn, ponieważ ma bezpośredni wpływ na komfort i bezpieczeństwo użytkowników. Projektanci muszą uwzględnić różnorodne czynniki, takie jak wysokość stanowiska pracy, dostępność narzędzi oraz sposób obsługi maszyny. Ważne jest, aby maszyna była dostosowana do indywidualnych potrzeb operatora, co może obejmować regulowane elementy sterujące czy odpowiednie oświetlenie miejsca pracy. Dobrze zaprojektowane stanowisko pracy minimalizuje ryzyko urazów oraz zmęczenia operatora podczas długotrwałej eksploatacji urządzenia. Kolejnym aspektem ergonomii jest intuicyjność obsługi maszyny – wszystkie przyciski i dźwignie powinny być łatwo dostępne i zrozumiałe dla użytkownika. Warto również zwrócić uwagę na materiały użyte do produkcji elementów maszyny, które powinny być przyjemne w dotyku i nie powodować dyskomfortu podczas pracy.
Jakie są wyzwania związane z nowoczesnym projektowaniem maszyn
Nowoczesne projektowanie maszyn wiąże się z wieloma wyzwaniami, które inżynierowie muszą pokonywać na każdym etapie procesu. Jednym z największych problemów jest konieczność dostosowania się do szybko zmieniających się technologii oraz potrzeb rynku. W miarę jak rozwijają się nowe materiały i metody produkcji, inżynierowie muszą być na bieżąco z najnowszymi trendami oraz innowacjami, aby móc tworzyć konkurencyjne produkty. Kolejnym wyzwaniem jest integracja różnych systemów technologicznych, takich jak automatyka czy robotyka, co wymaga ścisłej współpracy między różnymi specjalistami. Zrównoważony rozwój staje się coraz ważniejszym aspektem projektowania maszyn – inżynierowie muszą uwzględniać ekologiczne aspekty produkcji oraz eksploatacji urządzeń. Wreszcie, bezpieczeństwo użytkowników to priorytet w każdej fazie projektowania – inżynierowie muszą stosować się do rygorystycznych norm i przepisów dotyczących bezpieczeństwa pracy.
Jakie są kluczowe umiejętności potrzebne w projektowaniu maszyn
Projektowanie maszyn to dziedzina, która wymaga od inżynierów posiadania szerokiego wachlarza umiejętności technicznych oraz interpersonalnych. Przede wszystkim, niezbędna jest znajomość zasad mechaniki, materiałoznawstwa oraz technologii produkcji. Inżynierowie muszą być w stanie analizować i interpretować dane techniczne, co pozwala na podejmowanie trafnych decyzji projektowych. Umiejętność obsługi oprogramowania CAD oraz FEA jest również kluczowa, ponieważ to właśnie dzięki tym narzędziom można tworzyć precyzyjne modele i przeprowadzać analizy wytrzymałościowe. Ponadto, zdolności komunikacyjne są niezwykle ważne, ponieważ projektanci często współpracują z innymi specjalistami, takimi jak technicy, menedżerowie produkcji czy klienci. Umiejętność pracy w zespole oraz efektywna wymiana informacji mogą znacząco wpłynąć na jakość finalnego produktu. Wreszcie, elastyczność i zdolność do szybkiego przystosowywania się do zmieniających się warunków rynkowych są cechami, które mogą wyróżnić dobrego inżyniera w tej dynamicznej branży.
Jakie są najnowsze trendy w budowie maszyn i ich projektowaniu
W ostatnich latach branża budowy maszyn doświadcza wielu innowacji i trendów, które zmieniają sposób projektowania i produkcji urządzeń. Jednym z najważniejszych trendów jest automatyzacja procesów produkcyjnych, która pozwala na zwiększenie wydajności oraz redukcję kosztów. Wykorzystanie robotów przemysłowych staje się standardem w wielu zakładach produkcyjnych, co wpływa na jakość i precyzję wykonywanych operacji. Kolejnym istotnym trendem jest rozwój technologii cyfrowych, takich jak sztuczna inteligencja (AI) i uczenie maszynowe, które umożliwiają optymalizację procesów projektowania oraz produkcji. Dzięki tym technologiom możliwe jest przewidywanie awarii maszyn oraz dostosowywanie ich parametrów do bieżących potrzeb produkcyjnych. Również Internet Rzeczy (IoT) zyskuje na znaczeniu – połączenie maszyn z siecią pozwala na zbieranie danych w czasie rzeczywistym oraz monitorowanie ich pracy zdalnie. W kontekście zrównoważonego rozwoju coraz większą wagę przykłada się do ekologicznych aspektów produkcji – inżynierowie starają się wykorzystywać materiały odnawialne oraz minimalizować odpady produkcyjne.
Jakie są najczęstsze błędy popełniane podczas projektowania maszyn
Podczas projektowania maszyn inżynierowie mogą napotykać różnorodne pułapki i błędy, które mogą prowadzić do poważnych problemów w późniejszych etapach produkcji czy eksploatacji. Jednym z najczęstszych błędów jest niewłaściwe określenie wymagań klienta lub brak dokładnej analizy potrzeb użytkowników. To może skutkować stworzeniem maszyny, która nie spełnia oczekiwań lub ma ograniczoną funkcjonalność. Kolejnym powszechnym problemem jest niedostateczne uwzględnienie aspektów ergonomicznych – jeśli maszyna nie jest dostosowana do potrzeb operatora, może to prowadzić do dyskomfortu czy nawet urazów podczas pracy. Błędy w obliczeniach wytrzymałościowych lub niewłaściwy dobór materiałów również mogą mieć katastrofalne konsekwencje dla trwałości i bezpieczeństwa maszyny. Często spotykanym błędem jest także ignorowanie norm i przepisów dotyczących bezpieczeństwa pracy – brak zgodności z regulacjami może prowadzić do poważnych konsekwencji prawnych oraz finansowych. Wreszcie, nieodpowiednia komunikacja w zespole projektowym może prowadzić do nieporozumień i opóźnień w realizacji projektu.
Jakie są kluczowe czynniki wpływające na koszt budowy maszyn
Koszt budowy maszyn zależy od wielu czynników, które inżynierowie muszą brać pod uwagę już na etapie projektowania. Przede wszystkim należy uwzględnić koszty materiałów – wybór odpowiednich surowców ma kluczowe znaczenie dla całkowitych wydatków związanych z produkcją maszyny. Dodatkowo koszty robocizny stanowią istotny element budżetu; im bardziej skomplikowany proces produkcji, tym wyższe będą wydatki związane z zatrudnieniem specjalistów. Technologia używana w procesie produkcji również wpływa na koszty – nowoczesne maszyny wymagają często znacznych inwestycji w sprzęt oraz oprogramowanie CAD czy FEA. Warto również pamiętać o kosztach związanych z testowaniem prototypów oraz certyfikacją gotowych produktów; te etapy są niezbędne dla zapewnienia jakości i bezpieczeństwa urządzeń. Ostatecznie czynniki takie jak lokalizacja zakładu produkcyjnego czy dostępność wykwalifikowanej kadry również mają wpływ na całkowite koszty budowy maszyny.
Jakie są zalety korzystania z symulacji komputerowych w projektowaniu maszyn
Symulacje komputerowe stały się nieodłącznym elementem procesu projektowania maszyn, oferując szereg korzyści zarówno dla inżynierów, jak i producentów. Dzięki symulacjom możliwe jest przewidywanie zachowań maszyny w różnych warunkach bez konieczności tworzenia fizycznych prototypów, co znacznie przyspiesza proces projektowania i obniża koszty związane z testowaniem. Symulacje pozwalają na analizę wytrzymałości konstrukcji oraz identyfikację potencjalnych słabości jeszcze przed rozpoczęciem produkcji. Umożliwiają także optymalizację parametrów pracy maszyny poprzez analizę danych uzyskanych podczas symulacji różnych scenariuszy eksploatacyjnych. Dodatkowo wykorzystanie symulacji komputerowych sprzyja lepszemu komunikowaniu się między członkami zespołu projektowego – wizualizacja wyników symulacji ułatwia dyskusję na temat ewentualnych poprawek czy modyfikacji projektu. Co więcej, symulacje mogą być używane do szkolenia operatorów maszyn poprzez realistyczne odwzorowanie ich pracy w bezpiecznym środowisku wirtualnym.
Jakie są przyszłe kierunki rozwoju technologii w budowie maszyn
Przemysł budowy maszyn stoi przed wieloma wyzwaniami związanymi z dynamicznymi zmianami technologicznymi oraz rosnącymi wymaganiami rynku. W przyszłości możemy spodziewać się dalszego rozwoju automatyzacji procesów produkcyjnych – roboty będą coraz częściej wykorzystywane do wykonywania skomplikowanych operacji montażowych czy kontrolnych, co zwiększy efektywność i precyzję działań fabrycznych. Sztuczna inteligencja będzie odgrywać coraz większą rolę w analizie danych oraz optymalizacji procesów produkcyjnych; maszyny będą mogły uczyć się na podstawie zgromadzonych informacji i dostosowywać swoje parametry do zmieniających się warunków pracy. Zrównoważony rozwój stanie się priorytetem – inżynierowie będą poszukiwali ekologicznych materiałów oraz metod produkcji minimalizujących wpływ na środowisko naturalne. Internet Rzeczy (IoT) będzie kontynuował swoją ekspansję; połączenie maszyn z siecią pozwoli na zbieranie danych o ich pracy oraz prognozowanie awarii dzięki zastosowaniu zaawansowanych algorytmów analitycznych.