Robotyzacja i automatyzacja to kluczowe elementy, które w znaczący sposób wpływają na rozwój przemysłu 4.0. W dobie cyfryzacji, przedsiębiorstwa stają przed wyzwaniami związanymi z koniecznością dostosowania się do nowoczesnych technologii. Robotyzacja polega na wprowadzeniu robotów do procesów produkcyjnych, co pozwala na zwiększenie wydajności oraz precyzji działań. Automatyzacja natomiast odnosi się do zastosowania systemów informatycznych i technologii, które umożliwiają zautomatyzowanie różnych procesów, od produkcji po zarządzanie zasobami. Współczesne fabryki stają się coraz bardziej zautomatyzowane, co prowadzi do redukcji kosztów operacyjnych oraz poprawy jakości produktów. Dzięki zastosowaniu robotów, możliwe jest również zminimalizowanie ryzyka błędów ludzkich, co ma kluczowe znaczenie w branżach wymagających wysokiej precyzji, takich jak elektronika czy motoryzacja. W miarę jak technologia się rozwija, przedsiębiorstwa muszą inwestować w nowoczesne rozwiązania, aby nie zostać w tyle za konkurencją.
Jakie korzyści przynosi robotyzacja w przemyśle 4.0
Wprowadzenie robotyzacji do przemysłu 4.0 niesie ze sobą szereg korzyści, które mają istotny wpływ na efektywność produkcji oraz konkurencyjność firm. Przede wszystkim roboty są w stanie pracować przez długie godziny bez przerwy, co znacząco zwiększa wydajność linii produkcyjnych. Dzięki ich zastosowaniu można osiągnąć wyższą jakość produktów, ponieważ roboty wykonują zadania z dużą precyzją i powtarzalnością. Kolejną zaletą jest możliwość realizacji skomplikowanych zadań, które byłyby trudne lub wręcz niemożliwe do wykonania przez ludzi. Robotyzacja pozwala również na elastyczność produkcji – przedsiębiorstwa mogą szybko dostosować swoje linie produkcyjne do zmieniających się potrzeb rynku. Dodatkowo, automatyzacja procesów pozwala na lepsze zarządzanie danymi i analizę wyników produkcji w czasie rzeczywistym, co sprzyja podejmowaniu bardziej świadomych decyzji biznesowych.
Jakie wyzwania niesie ze sobą automatyzacja przemysłu 4.0
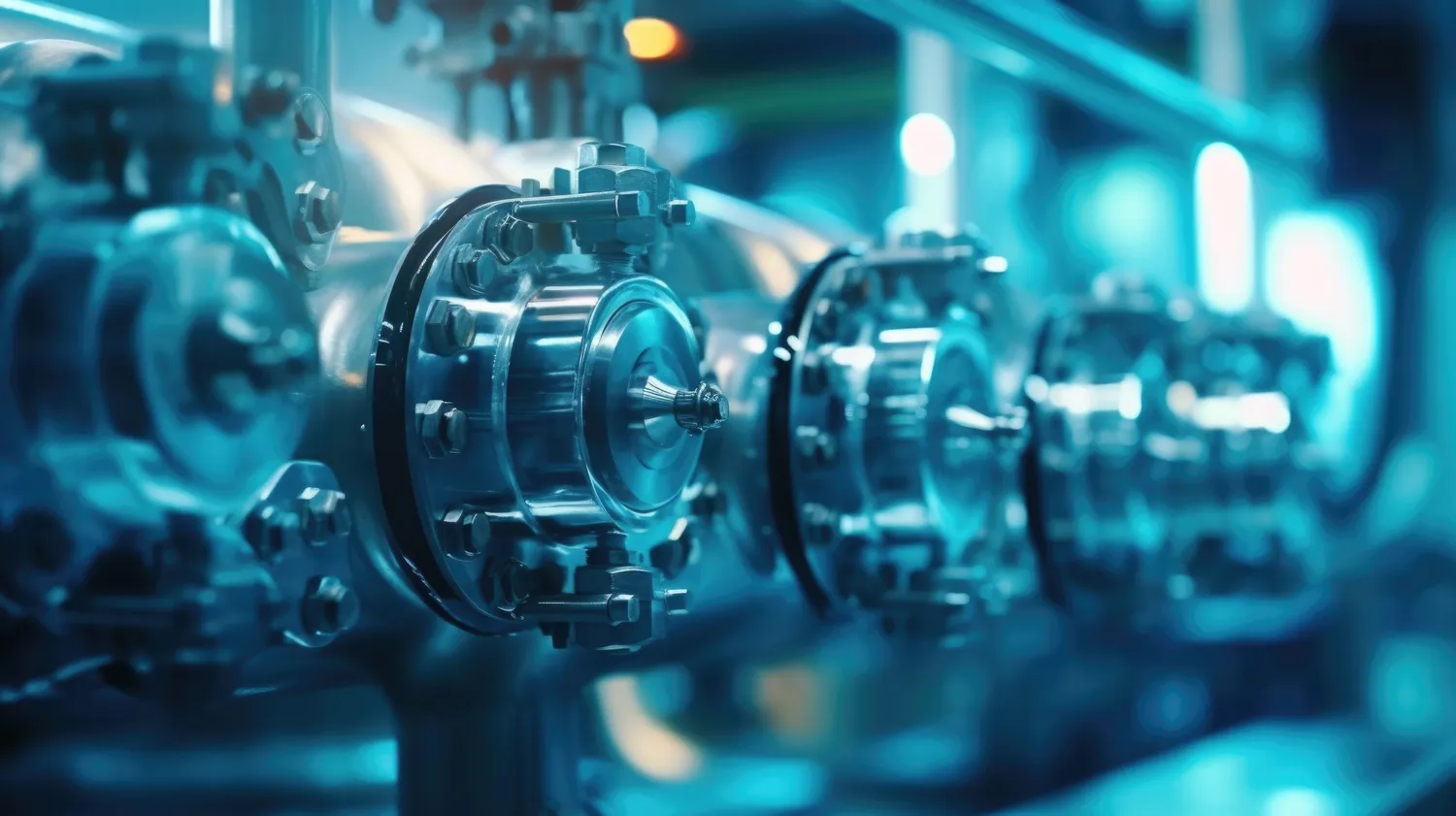
Mimo licznych korzyści płynących z automatyzacji w przemyśle 4.0, istnieje również szereg wyzwań, które przedsiębiorstwa muszą stawić czoła podczas wdrażania nowych technologii. Jednym z głównych problemów jest potrzeba przeszkolenia pracowników, którzy będą musieli nauczyć się obsługi nowych systemów oraz technologii. W wielu przypadkach może to prowadzić do oporu ze strony załogi, która obawia się utraty pracy na rzecz maszyn. Kolejnym wyzwaniem jest wysoki koszt początkowy związany z zakupem i wdrożeniem nowoczesnych rozwiązań technologicznych. Firmy muszą dokładnie przeanalizować swoje możliwości finansowe oraz zwrot z inwestycji związanych z automatyzacją procesów. Dodatkowo, integracja nowych systemów z istniejącymi infrastrukturami może być skomplikowana i czasochłonna, co może opóźnić pełne wdrożenie automatyzacji. Istotnym aspektem jest również zapewnienie bezpieczeństwa danych oraz ochrony przed cyberatakami, które stają się coraz większym zagrożeniem dla przedsiębiorstw korzystających z nowoczesnych technologii.
Jakie technologie wspierają robotyzację i automatyzację przemysłu 4.0
W kontekście robotyzacji i automatyzacji przemysłu 4.0 kluczowe znaczenie mają różnorodne technologie, które wspierają te procesy i umożliwiają ich efektywne wdrażanie. Jedną z najważniejszych technologii jest Internet Rzeczy (IoT), który pozwala na komunikację między urządzeniami oraz zbieranie danych w czasie rzeczywistym. Dzięki IoT możliwe jest monitorowanie procesów produkcyjnych oraz optymalizacja ich przebiegu poprzez analizę zgromadzonych informacji. Kolejnym istotnym elementem są systemy sztucznej inteligencji (AI), które mogą być wykorzystywane do analizy danych oraz podejmowania decyzji na podstawie zgromadzonych informacji. AI umożliwia także rozwój autonomicznych robotów zdolnych do samodzielnego wykonywania skomplikowanych zadań bez potrzeby interwencji człowieka. Również technologia chmurowa odgrywa kluczową rolę w automatyzacji procesów biznesowych poprzez umożliwienie przechowywania danych oraz ich analizy na dużą skalę. Warto również wspomnieć o systemach zarządzania produkcją (MES), które integrują różne aspekty procesu produkcyjnego i pozwalają na jego optymalizację poprzez bieżące monitorowanie oraz analizę wyników produkcji.
Jak robotyzacja wpływa na zatrudnienie w przemyśle 4.0
Robotyzacja w przemyśle 4.0 ma znaczący wpływ na rynek pracy, co budzi wiele emocji i kontrowersji. Z jednej strony, automatyzacja procesów produkcyjnych prowadzi do redukcji miejsc pracy, szczególnie w sektorach, gdzie zadania są rutynowe i powtarzalne. W wielu przypadkach roboty mogą zastąpić pracowników wykonujących proste prace manualne, co może prowadzić do obaw o przyszłość zatrudnienia w tych branżach. Z drugiej strony, rozwój technologii stwarza nowe możliwości zatrudnienia w obszarach związanych z projektowaniem, programowaniem oraz utrzymaniem systemów automatyzacji. Pracownicy będą musieli dostosować swoje umiejętności do zmieniających się warunków rynkowych, co może prowadzić do wzrostu zapotrzebowania na specjalistów w dziedzinie IT oraz inżynierii. Warto również zauważyć, że robotyzacja może przyczynić się do poprawy warunków pracy, eliminując niebezpieczne lub monotonne zadania, które mogą być szkodliwe dla zdrowia pracowników. Firmy powinny inwestować w programy szkoleniowe, aby pomóc pracownikom w adaptacji do nowej rzeczywistości oraz umożliwić im rozwój zawodowy w obszarach związanych z nowymi technologiami.
Jakie są przykłady zastosowania robotyzacji w różnych branżach
Robotyzacja znajduje zastosowanie w wielu branżach, a jej wpływ na efektywność produkcji oraz jakość produktów jest widoczny na każdym kroku. W przemyśle motoryzacyjnym roboty odgrywają kluczową rolę w montażu pojazdów, gdzie są wykorzystywane do spawania, malowania oraz montażu komponentów. Dzięki ich zastosowaniu możliwe jest osiągnięcie wysokiej precyzji i powtarzalności procesów produkcyjnych. W branży elektronicznej roboty są wykorzystywane do montażu delikatnych komponentów, takich jak układy scalone czy płyty główne, gdzie precyzja jest kluczowa. W sektorze spożywczym automatyzacja procesów pakowania oraz sortowania produktów znacznie zwiększa wydajność linii produkcyjnych. Również w logistyce roboty autonomiczne są wykorzystywane do transportu towarów wewnątrz magazynów oraz do realizacji zamówień online. Przykładem mogą być systemy magazynowe Amazon, które wykorzystują roboty do optymalizacji procesu kompletacji zamówień. W medycynie roboty chirurgiczne stają się coraz bardziej popularne, umożliwiając przeprowadzanie skomplikowanych operacji z większą precyzją i mniejszym ryzykiem powikłań.
Jakie są przyszłe trendy w robotyzacji i automatyzacji przemysłu 4.0
Przemysł 4.0 to dynamicznie rozwijający się obszar, który nieustannie ewoluuje pod wpływem nowych technologii oraz zmieniających się potrzeb rynku. Wśród przyszłych trendów związanych z robotyzacją i automatyzacją można wyróżnić rosnącą integrację sztucznej inteligencji z systemami automatyzacji. AI pozwala na tworzenie bardziej zaawansowanych algorytmów analitycznych, które mogą przewidywać awarie maszyn czy optymalizować procesy produkcyjne na podstawie danych zebranych w czasie rzeczywistym. Kolejnym istotnym trendem jest rozwój współpracy między ludźmi a robotami, co prowadzi do powstawania tzw. cobotów – robotów współpracujących z pracownikami na linii produkcyjnej. Coboty są projektowane tak, aby mogły bezpiecznie pracować obok ludzi i wspierać ich w wykonywaniu różnorodnych zadań. Również technologia chmurowa będzie odgrywać coraz większą rolę w automatyzacji procesów biznesowych, umożliwiając dostęp do danych oraz aplikacji z dowolnego miejsca na świecie. Dodatkowo rozwój Internetu Rzeczy (IoT) sprawi, że maszyny będą mogły komunikować się ze sobą i wymieniać dane w czasie rzeczywistym, co przyczyni się do jeszcze większej efektywności procesów produkcyjnych.
Jakie wyzwania stoją przed przedsiębiorstwami wdrażającymi przemysł 4.0
Wdrażanie przemysłu 4.0 wiąże się z wieloma wyzwaniami, które przedsiębiorstwa muszą pokonać, aby skutecznie wykorzystać potencjał robotyzacji i automatyzacji. Jednym z głównych problemów jest zapewnienie odpowiedniej infrastruktury technologicznej, która umożliwi integrację nowych systemów z istniejącymi rozwiązaniami. Firmy muszą inwestować w modernizację swoich zakładów produkcyjnych oraz zakup nowoczesnych urządzeń i oprogramowania. Kolejnym wyzwaniem jest zarządzanie danymi – przedsiębiorstwa muszą opracować strategie dotyczące gromadzenia, przechowywania oraz analizy danych generowanych przez maszyny i systemy automatyzacyjne. Bez odpowiednich narzędzi analitycznych trudno będzie wykorzystać pełen potencjał zbieranych informacji. Również bezpieczeństwo cybernetyczne staje się kluczowym zagadnieniem – wraz z rosnącą liczbą połączonych urządzeń wzrasta ryzyko ataków hakerskich oraz kradzieży danych. Firmy muszą inwestować w zabezpieczenia oraz edukację pracowników w zakresie ochrony danych osobowych i informacji poufnych.
Jakie są kluczowe umiejętności potrzebne w erze przemysłu 4.0
W erze przemysłu 4.0 kluczowe znaczenie mają umiejętności dostosowane do nowoczesnych technologii oraz zmieniających się warunków rynkowych. Pracownicy muszą posiadać umiejętności techniczne związane z obsługą maszyn oraz systemów automatyzacyjnych – znajomość programowania czy analizy danych staje się niezbędna w wielu branżach. Również umiejętność pracy z nowoczesnymi narzędziami informatycznymi oraz systemami zarządzania produkcją jest niezwykle istotna dla efektywnego funkcjonowania przedsiębiorstw. Oprócz umiejętności technicznych ważne są również kompetencje miękkie – zdolność do pracy zespołowej, komunikacji oraz kreatywnego myślenia stają się kluczowe w kontekście współpracy między ludźmi a robotami. Pracownicy powinni być otwarci na naukę i rozwój osobisty, aby móc dostosować swoje umiejętności do zmieniających się wymagań rynku pracy.