Destylacja rozpuszczalników to proces, który odgrywa kluczową rolę w chemii oraz przemyśle chemicznym. Jest to technika separacji substancji na podstawie różnicy w temperaturach wrzenia. W praktyce oznacza to, że podczas podgrzewania mieszaniny cieczy, składniki o niższej temperaturze wrzenia odparowują jako pierwsze, a następnie są skraplane i zbierane w osobnym naczyniu. Proces ten może być stosowany do oczyszczania rozpuszczalników, usuwania zanieczyszczeń lub odzyskiwania cennych substancji chemicznych. Kluczowym elementem tego procesu jest zastosowanie odpowiedniego sprzętu, takiego jak kolumna destylacyjna czy aparat destylacyjny. Warto również zwrócić uwagę na czynniki wpływające na efektywność destylacji, takie jak ciśnienie atmosferyczne, które może zmieniać temperatury wrzenia substancji.
Jakie są różne metody destylacji rozpuszczalników
W kontekście destylacji rozpuszczalników istnieje kilka różnych metod, które można zastosować w zależności od specyfiki procesu oraz rodzaju substancji. Najpopularniejszą metodą jest destylacja prosta, która jest idealna do separacji substancji o znacznej różnicy temperatur wrzenia. Kolejną metodą jest destylacja frakcyjna, która pozwala na oddzielenie kilku składników z mieszaniny o zbliżonych temperaturach wrzenia. W tej metodzie wykorzystuje się kolumny frakcyjne, które zwiększają efektywność separacji poprzez wielokrotne skraplanie i odparowywanie składników. Istnieje także destylacja azeotropowa, która jest stosowana w przypadku mieszanin tworzących azeotropy, czyli mieszaniny o stałym składzie, które mają tę samą temperaturę wrzenia. Ponadto wyróżniamy destylację pod ciśnieniem atmosferycznym oraz pod próżnią, co ma znaczenie w przypadku substancji wrażliwych na wysoką temperaturę.
Jakie są zastosowania destylacji rozpuszczalników w przemyśle
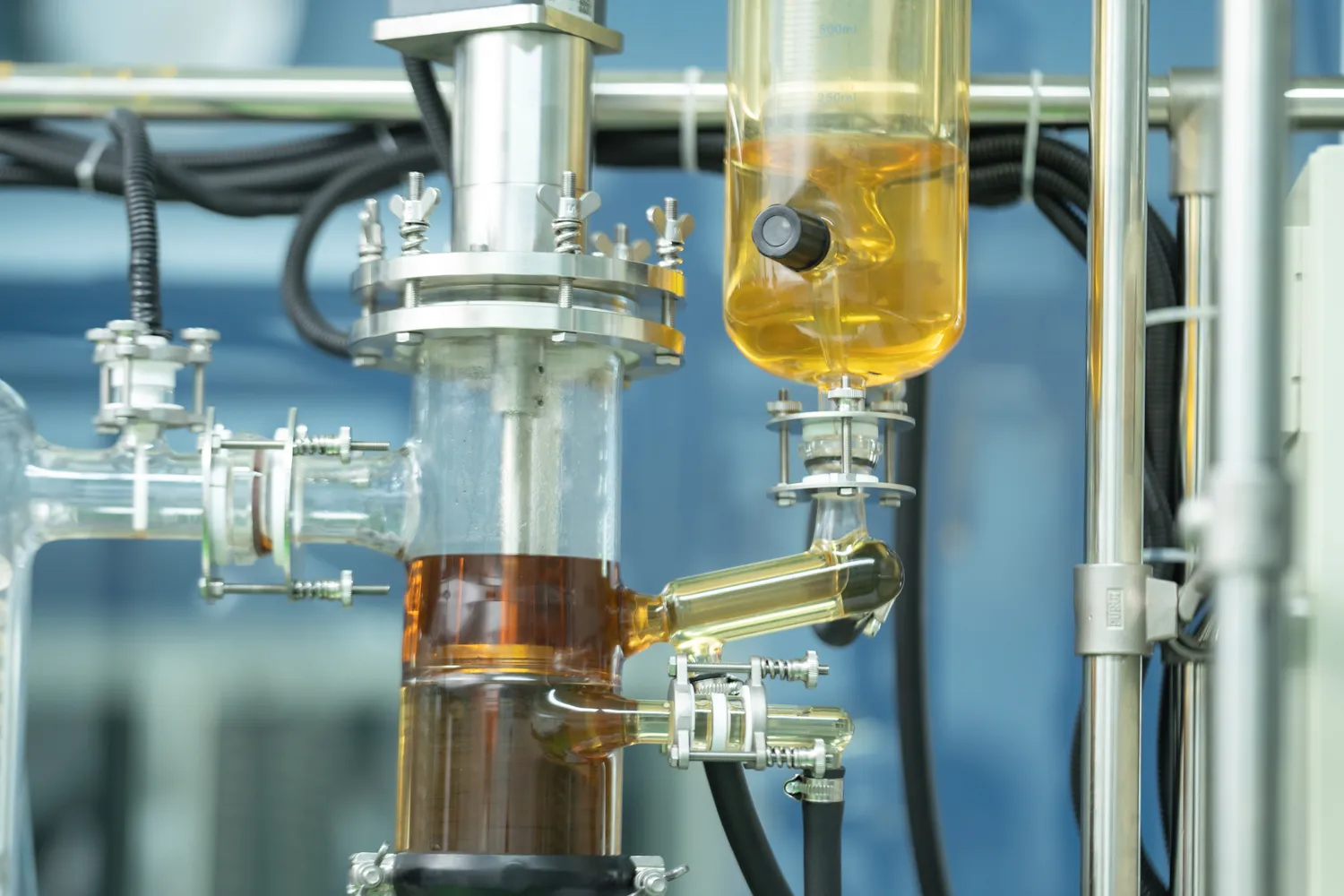
Destylacja rozpuszczalników znajduje szerokie zastosowanie w różnych gałęziach przemysłu chemicznego oraz farmaceutycznego. W przemyśle chemicznym proces ten jest często wykorzystywany do oczyszczania surowców oraz produktów końcowych. Na przykład wiele organicznych rozpuszczalników, takich jak etanol czy aceton, wymaga oczyszczenia przed użyciem w syntezach chemicznych. W przemyśle petrochemicznym destylacja jest kluczowym etapem w procesie rafinacji ropy naftowej, gdzie różne frakcje paliwowe są oddzielane na podstawie ich temperatur wrzenia. W farmacji natomiast destylacja służy do produkcji czystych substancji czynnych oraz ich formułowania w lekach. Ponadto proces ten jest wykorzystywany w produkcji alkoholi spożywczych, gdzie fermentowane surowce są poddawane destylacji w celu uzyskania wysokoprocentowych napojów alkoholowych.
Jakie są wyzwania związane z destylacją rozpuszczalników
Pomimo licznych zalet, destylacja rozpuszczalników wiąże się również z pewnymi wyzwaniami i ograniczeniami. Jednym z głównych problemów jest konieczność precyzyjnego kontrolowania warunków procesu, takich jak temperatura i ciśnienie. Niewłaściwe ustawienia mogą prowadzić do nieefektywnej separacji lub nawet degradacji cennych substancji chemicznych. Kolejnym wyzwaniem jest kwestia bezpieczeństwa; wiele rozpuszczalników jest łatwopalnych lub toksycznych, co wymaga zachowania szczególnej ostrożności podczas przeprowadzania procesu. Dodatkowo koszty związane z zakupem sprzętu oraz eksploatacją systemów destylacyjnych mogą być znaczne, co stanowi barierę dla mniejszych przedsiębiorstw. Wreszcie należy pamiętać o wpływie procesu na środowisko; niektóre metody mogą generować odpady lub emisje szkodliwych substancji do atmosfery.
Jakie są kluczowe etapy procesu destylacji rozpuszczalników
Proces destylacji rozpuszczalników składa się z kilku kluczowych etapów, które są niezbędne do skutecznego oddzielenia składników mieszaniny. Pierwszym krokiem jest przygotowanie surowca, który może wymagać wstępnego oczyszczenia lub filtracji, aby usunąć większe zanieczyszczenia. Następnie następuje podgrzewanie cieczy w odpowiednim naczyniu, co prowadzi do odparowania substancji o niższej temperaturze wrzenia. W tym momencie ważne jest, aby monitorować temperaturę, aby zapewnić optymalne warunki dla separacji. Odparowane cząsteczki przechodzą następnie do kondensatora, gdzie schładzane są i skraplają się, tworząc ciecz. Skroplona substancja jest zbierana w osobnym naczyniu, co pozwala na uzyskanie oczyszczonego rozpuszczalnika. W przypadku destylacji frakcyjnej proces ten jest bardziej złożony i wymaga zastosowania kolumny frakcyjnej, która umożliwia wielokrotne skraplanie i odparowywanie, co zwiększa efektywność separacji.
Jakie są różnice między destylacją a innymi metodami separacji
Destylacja rozpuszczalników to jedna z wielu metod separacji substancji chemicznych, ale różni się ona od innych technik pod względem zasad działania oraz zastosowań. Na przykład jedną z alternatywnych metod jest ekstrakcja, która polega na wykorzystaniu rozpuszczalników do wydobywania określonych składników z mieszaniny. W przeciwieństwie do destylacji, ekstrakcja nie opiera się na różnicy temperatur wrzenia, lecz na różnicy rozpuszczalności składników w różnych rozpuszczalnikach. Inną popularną metodą jest filtracja, która polega na oddzielaniu ciał stałych od cieczy za pomocą materiału filtracyjnego. Filtracja jest skuteczna w przypadku mieszanin zawierających cząstki stałe, ale nie nadaje się do separacji cieczy o podobnych właściwościach fizykochemicznych. Z kolei chromatografia to kolejna technika separacyjna, która wykorzystuje różnice w interakcjach składników z fazą stacjonarną i ruchomą. Jest to metoda bardziej skomplikowana i czasochłonna niż destylacja, ale pozwala na uzyskanie bardzo czystych frakcji.
Jakie są najnowsze osiągnięcia w technologii destylacji rozpuszczalników
W ostatnich latach technologia destylacji rozpuszczalników przeszła znaczące zmiany dzięki postępom w dziedzinie inżynierii chemicznej oraz technologii materiałowej. Jednym z najważniejszych osiągnięć jest rozwój nowoczesnych kolumn destylacyjnych, które charakteryzują się wyższą efektywnością separacyjną oraz mniejszym zużyciem energii. Dzięki zastosowaniu innowacyjnych materiałów i konstrukcji możliwe jest osiągnięcie lepszych wyników przy mniejszych kosztach operacyjnych. Ponadto coraz częściej stosuje się technologie automatyzacji i monitorowania procesów destylacyjnych, co pozwala na precyzyjniejsze kontrolowanie warunków pracy oraz szybsze reagowanie na ewentualne problemy. Warto również zwrócić uwagę na rozwój ekologicznych metod destylacji, takich jak destylacja osmotyczna czy wykorzystanie energii słonecznej do podgrzewania cieczy. Te nowe podejścia mają na celu zmniejszenie wpływu procesów chemicznych na środowisko oraz poprawę efektywności energetycznej całego procesu.
Jakie są najczęstsze błędy podczas destylacji rozpuszczalników
Podczas przeprowadzania procesu destylacji rozpuszczalników mogą wystąpić różne błędy, które mogą negatywnie wpłynąć na jakość uzyskanych produktów oraz efektywność całego procesu. Jednym z najczęstszych problemów jest niewłaściwe ustawienie temperatury podgrzewania, co może prowadzić do nieefektywnej separacji składników lub ich degradacji. Inny błąd to brak odpowiedniego monitorowania ciśnienia atmosferycznego; zmiany ciśnienia mogą znacząco wpłynąć na temperatury wrzenia substancji i skutkować nieprzewidywalnymi rezultatami. Ponadto wielu operatorów pomija konieczność regularnego czyszczenia sprzętu destylacyjnego; nagromadzenie zanieczyszczeń może prowadzić do obniżenia wydajności oraz jakości produktów końcowych. Ważne jest również przeprowadzenie analizy jakości uzyskanych frakcji; niedostateczna kontrola jakości może skutkować użyciem nieodpowiednich lub zanieczyszczonych substancji w dalszych procesach produkcyjnych.
Jakie są przyszłe kierunki badań nad destylacją rozpuszczalników
W miarę jak przemysł chemiczny ewoluuje i dostosowuje się do zmieniających się potrzeb rynkowych oraz wymogów ochrony środowiska, badania nad destylacją rozpuszczalników koncentrują się na kilku kluczowych obszarach. Jednym z nich jest rozwój bardziej efektywnych i ekologicznych technologii separacyjnych, które minimalizują zużycie energii oraz ograniczają emisję szkodliwych substancji do atmosfery. Badania te obejmują zarówno doskonalenie istniejących metod destylacji, jak i poszukiwanie nowych podejść opartych na alternatywnych zasadach fizycznych czy chemicznych. Kolejnym ważnym kierunkiem badań jest integracja procesów chemicznych z odnawialnymi źródłami energii; wykorzystanie energii słonecznej czy geotermalnej w procesach destylacyjnych może znacząco zmniejszyć ich ślad węglowy. Ponadto naukowcy pracują nad nowymi materiałami dla kolumn destylacyjnych oraz kondensatorów, które mogłyby poprawić efektywność separacyjną i skrócić czas procesu.
Jakie są kluczowe czynniki wpływające na efektywność destylacji rozpuszczalników
Efektywność destylacji rozpuszczalników zależy od wielu czynników, które należy starannie kontrolować, aby uzyskać optymalne wyniki. Jednym z najważniejszych elementów jest temperatura podgrzewania; zbyt niska temperatura może prowadzić do niepełnej separacji, podczas gdy zbyt wysoka może powodować degradację składników. Również ciśnienie atmosferyczne ma istotny wpływ na proces; w przypadku destylacji pod próżnią można obniżyć temperatury wrzenia, co jest korzystne dla substancji wrażliwych na wysoką temperaturę. Kolejnym czynnikiem jest konstrukcja kolumny destylacyjnej; odpowiednio zaprojektowane elementy, takie jak wypełnienie kolumny czy liczba teoretycznych półek, mogą znacząco zwiększyć wydajność procesu. Ważne jest również dobranie odpowiednich materiałów do budowy sprzętu, które będą odporne na działanie chemikaliów oraz wysokich temperatur.