Budowa maszyn roboczych to złożony proces, który wymaga uwzględnienia wielu kluczowych elementów. Wśród nich wyróżnia się układ napędowy, który jest odpowiedzialny za generowanie mocy i przekazywanie jej na inne części maszyny. Zazwyczaj składa się on z silnika, przekładni oraz systemu przeniesienia napędu. Kolejnym istotnym elementem jest układ roboczy, który wykonuje konkretne zadania, takie jak cięcie, spawanie czy formowanie. W zależności od przeznaczenia maszyny, układ roboczy może być różnie skonstruowany, co wpływa na jego wydajność i efektywność działania. Ważnym aspektem jest również konstrukcja nośna, która zapewnia stabilność i wytrzymałość całej maszyny. Wykonana zazwyczaj z metalu lub kompozytów, musi być odpowiednio zaprojektowana, aby wytrzymać obciążenia podczas pracy. Nie można zapomnieć o systemach sterowania, które umożliwiają operatorowi kontrolowanie maszyny oraz monitorowanie jej pracy.
Jakie materiały są wykorzystywane w budowie maszyn roboczych
W budowie maszyn roboczych kluczową rolę odgrywają materiały, które muszą spełniać określone wymagania dotyczące wytrzymałości, trwałości oraz odporności na różne czynniki zewnętrzne. Najczęściej stosowanym materiałem jest stal, ze względu na swoje właściwości mechaniczne oraz łatwość obróbczości. Stal węglowa jest powszechnie używana w elementach nośnych oraz w układzie roboczym maszyn. Oprócz stali wykorzystuje się także aluminium, które charakteryzuje się niską wagą oraz wysoką odpornością na korozję. Aluminium znajduje zastosowanie w konstrukcjach, gdzie istotne jest zmniejszenie masy maszyny bez utraty jej wytrzymałości. W przypadku elementów narażonych na wysokie temperatury lub agresywne chemikalia stosuje się materiały kompozytowe oraz stopy metali odpornych na korozję. W ostatnich latach rośnie zainteresowanie tworzywami sztucznymi, które dzięki swoim właściwościom izolacyjnym i odporności na działanie różnych substancji chemicznych znajdują zastosowanie w wielu komponentach maszyn.
Jakie są najnowsze technologie w budowie maszyn roboczych
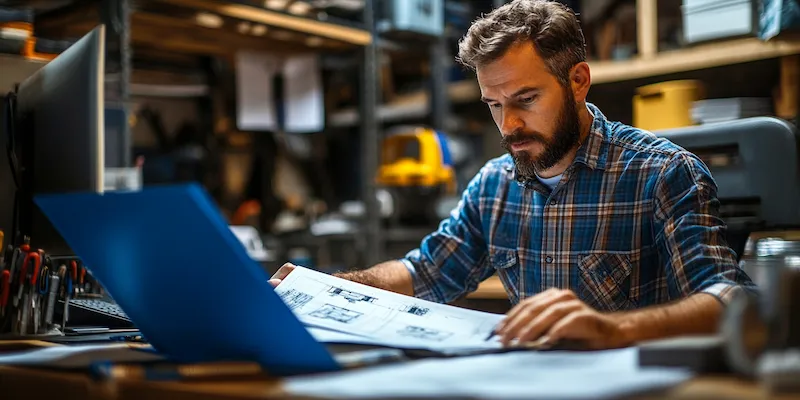
W ostatnich latach nastąpił dynamiczny rozwój technologii związanych z budową maszyn roboczych, co znacząco wpłynęło na ich funkcjonalność i efektywność. Jednym z najważniejszych trendów jest automatyzacja procesów produkcyjnych, która pozwala na zwiększenie wydajności oraz redukcję kosztów operacyjnych. Dzięki zastosowaniu robotów przemysłowych możliwe stało się zautomatyzowanie wielu czynności, które wcześniej wymagały pracy ludzkiej. Kolejnym istotnym aspektem jest rozwój technologii cyfrowych oraz Internetu rzeczy (IoT), które umożliwiają zdalne monitorowanie i zarządzanie maszynami w czasie rzeczywistym. Dzięki temu operatorzy mogą szybko reagować na ewentualne awarie czy problemy techniczne. Wprowadzenie systemów sztucznej inteligencji do procesów projektowania i produkcji maszyn pozwala na optymalizację ich parametrów oraz dostosowywanie do indywidualnych potrzeb użytkowników. Również technologie druku 3D zaczynają odgrywać coraz większą rolę w budowie maszyn roboczych, umożliwiając szybkie prototypowanie oraz produkcję skomplikowanych komponentów o niewielkiej wadze i dużej wytrzymałości.
Jakie są zastosowania maszyn roboczych w różnych branżach
Maszyny robocze znajdują szerokie zastosowanie w różnych branżach przemysłu, co czyni je niezbędnym elementem nowoczesnej produkcji. W przemyśle budowlanym wykorzystuje się maszyny takie jak koparki czy dźwigi, które ułatwiają wykonywanie ciężkich prac ziemnych oraz transport materiałów budowlanych. W sektorze motoryzacyjnym maszyny robocze są wykorzystywane do montażu pojazdów oraz obróbki komponentów silnikowych. Przemysł spożywczy korzysta z maszyn do pakowania, sortowania oraz przetwarzania żywności, co zwiększa efektywność produkcji i zapewnia wysoką jakość produktów końcowych. Również w branży elektronicznej maszyny odgrywają kluczową rolę w procesach montażu i testowania podzespołów elektronicznych. W rolnictwie nowoczesne maszyny robocze takie jak traktory czy kombajny znacznie usprawniają prace polowe oraz zbiorowe plonów. Zastosowanie technologii automatyzacji sprawia, że maszyny te stają się coraz bardziej precyzyjne i wydajne, co przekłada się na wzrost plonów oraz oszczędność czasu pracy rolników.
Jakie są kluczowe wyzwania w budowie maszyn roboczych
Budowa maszyn roboczych wiąże się z wieloma wyzwaniami, które mogą wpłynąć na jakość i efektywność końcowego produktu. Jednym z głównych problemów jest konieczność dostosowania maszyn do zmieniających się potrzeb rynku oraz wymagań klientów. W dobie szybkiego rozwoju technologii i rosnącej konkurencji, producenci muszą nieustannie innowować swoje rozwiązania, aby sprostać oczekiwaniom użytkowników. Kolejnym wyzwaniem jest zapewnienie wysokiej jakości materiałów oraz komponentów, które są kluczowe dla trwałości i niezawodności maszyn. W obliczu globalizacji łańcuchów dostaw, producenci muszą dbać o to, aby materiały spełniały określone normy jakościowe oraz były dostępne w odpowiednich ilościach. Problemy związane z dostępnością surowców mogą prowadzić do opóźnień w produkcji oraz zwiększenia kosztów. Również kwestie związane z ekologią i zrównoważonym rozwojem stają się coraz ważniejsze w kontekście budowy maszyn roboczych. Producenci muszą dążyć do minimalizacji wpływu swoich produktów na środowisko, co często wymaga zastosowania nowych technologii oraz materiałów.
Jakie są przyszłe kierunki rozwoju budowy maszyn roboczych
Przyszłość budowy maszyn roboczych zapowiada się niezwykle interesująco, z uwagi na dynamiczny rozwój technologii oraz zmieniające się potrzeby rynku. Jednym z kluczowych kierunków rozwoju jest dalsza automatyzacja procesów produkcyjnych, która pozwoli na zwiększenie wydajności oraz redukcję kosztów pracy. W miarę jak technologia robotyki staje się coraz bardziej zaawansowana, maszyny będą mogły wykonywać coraz bardziej skomplikowane zadania, co otworzy nowe możliwości dla przemysłu. Kolejnym istotnym trendem jest integracja systemów sztucznej inteligencji w procesach projektowania i produkcji maszyn. Dzięki AI możliwe będzie optymalizowanie parametrów pracy maszyn oraz przewidywanie ewentualnych awarii, co przyczyni się do zwiększenia ich niezawodności. Również rozwój Internetu rzeczy (IoT) będzie miał znaczący wpływ na przyszłość budowy maszyn roboczych, umożliwiając zdalne monitorowanie ich pracy oraz zbieranie danych analitycznych dotyczących efektywności działania. W kontekście ochrony środowiska coraz większe znaczenie będą miały technologie związane z ekologicznymi rozwiązaniami w budowie maszyn, takie jak wykorzystanie materiałów biodegradowalnych czy energooszczędnych układów napędowych.
Jakie są różnice między różnymi typami maszyn roboczych
Maszyny robocze można klasyfikować według różnych kryteriów, co prowadzi do powstania wielu typów urządzeń o odmiennych właściwościach i zastosowaniach. Jednym z podstawowych podziałów jest klasyfikacja według rodzaju napędu, gdzie wyróżnia się maszyny elektryczne, hydrauliczne oraz pneumatyczne. Maszyny elektryczne charakteryzują się wysoką efektywnością energetyczną i niskim poziomem hałasu, co sprawia, że są popularne w wielu branżach przemysłowych. Z kolei maszyny hydrauliczne oferują dużą siłę roboczą przy stosunkowo niewielkich rozmiarach, co czyni je idealnymi do zastosowań wymagających dużej mocy w ograniczonej przestrzeni. Maszyny pneumatyczne natomiast wykorzystują sprężone powietrze jako medium robocze i znajdują zastosowanie tam, gdzie istotna jest szybkość działania oraz precyzja. Innym kryterium podziału jest przeznaczenie maszyny – można wyróżnić maszyny do obróbki metali, maszyny budowlane czy maszyny rolnicze. Każdy z tych typów ma swoje specyficzne wymagania dotyczące konstrukcji i materiałów użytych do produkcji.
Jakie są korzyści płynące z modernizacji maszyn roboczych
Modernizacja maszyn roboczych to proces, który przynosi wiele korzyści zarówno dla producentów, jak i użytkowników tych urządzeń. Przede wszystkim modernizacja pozwala na zwiększenie wydajności pracy maszyn poprzez zastosowanie nowoczesnych technologii oraz komponentów o lepszych parametrach technicznych. Dzięki temu możliwe jest osiągnięcie lepszej jakości produktów końcowych oraz skrócenie czasu produkcji. Kolejną korzyścią jest poprawa bezpieczeństwa pracy operatorów dzięki wprowadzeniu nowoczesnych systemów sterowania oraz zabezpieczeń. Nowe technologie pozwalają na monitorowanie stanu maszyny w czasie rzeczywistym oraz szybsze reagowanie na ewentualne awarie czy nieprawidłowości w działaniu. Modernizacja może również przyczynić się do zmniejszenia kosztów eksploatacji poprzez zastosowanie energooszczędnych rozwiązań oraz materiałów o dłuższej żywotności. Warto również zauważyć, że modernizacja maszyn może pozytywnie wpłynąć na wizerunek firmy jako innowacyjnego producenta dbającego o jakość swoich produktów oraz środowisko naturalne.
Jakie są najważniejsze standardy jakości w budowie maszyn roboczych
W budowie maszyn roboczych kluczową rolę odgrywają standardy jakości, które mają na celu zapewnienie bezpieczeństwa użytkowników oraz niezawodności działania urządzeń. Jednym z najważniejszych standardów jest norma ISO 9001, która dotyczy systemu zarządzania jakością i obejmuje wszystkie etapy produkcji – od projektowania po dostawę gotowego produktu. Przestrzeganie tej normy pozwala firmom na ciągłe doskonalenie procesów oraz zwiększenie satysfakcji klientów poprzez dostarczanie produktów spełniających określone wymagania jakościowe. Innym istotnym standardem jest norma ISO 14001 dotycząca zarządzania środowiskowego, która nakłada obowiązek minimalizacji negatywnego wpływu działalności przedsiębiorstwa na środowisko naturalne. W przypadku maszyn roboczych szczególną uwagę zwraca się także na normy bezpieczeństwa takie jak CE czy ANSI, które potwierdzają zgodność produktów z obowiązującymi przepisami prawa dotyczącymi bezpieczeństwa użytkowania. Dodatkowo wiele branż posiada swoje specyficzne normy i standardy jakościowe, które muszą być spełnione przez producentów maszyn roboczych działających w danej dziedzinie przemysłu.