Przemysł 4.0 to termin, który odnosi się do czwartej rewolucji przemysłowej, charakteryzującej się integracją nowoczesnych technologii w procesach produkcyjnych. W przeciwieństwie do wcześniejszych rewolucji, które skupiały się głównie na mechanizacji i automatyzacji, przemysł 4.0 wprowadza zaawansowane technologie informacyjne oraz komunikacyjne do fabryk i zakładów produkcyjnych. Kluczowymi elementami tego zjawiska są Internet rzeczy, sztuczna inteligencja, big data oraz robotyka. Dzięki tym technologiom możliwe jest nie tylko zwiększenie efektywności produkcji, ale także poprawa jakości produktów oraz elastyczność procesów w odpowiedzi na zmieniające się potrzeby rynku. Przemysł 4.0 stawia również na zrównoważony rozwój, co oznacza dążenie do minimalizacji wpływu działalności przemysłowej na środowisko naturalne.
Jakie technologie są kluczowe w przemyśle 4.0?
W kontekście przemysłu 4.0 kluczowe technologie obejmują szereg innowacji, które mają na celu usprawnienie procesów produkcyjnych oraz zarządzania. Internet rzeczy (IoT) pozwala na połączenie maszyn i urządzeń w sieć, co umożliwia zbieranie danych w czasie rzeczywistym oraz ich analizę. Sztuczna inteligencja (AI) odgrywa istotną rolę w przetwarzaniu tych danych, co pozwala na podejmowanie szybkich decyzji oraz przewidywanie awarii czy potrzeb serwisowych. Big data to kolejny ważny element, który umożliwia analizę ogromnych zbiorów danych generowanych przez maszyny i systemy produkcyjne. Robotyka również zyskuje na znaczeniu, gdyż nowoczesne roboty są coraz bardziej autonomiczne i zdolne do wykonywania skomplikowanych zadań w dynamicznych warunkach produkcyjnych.
Jakie korzyści przynosi wdrożenie przemysłu 4.0?
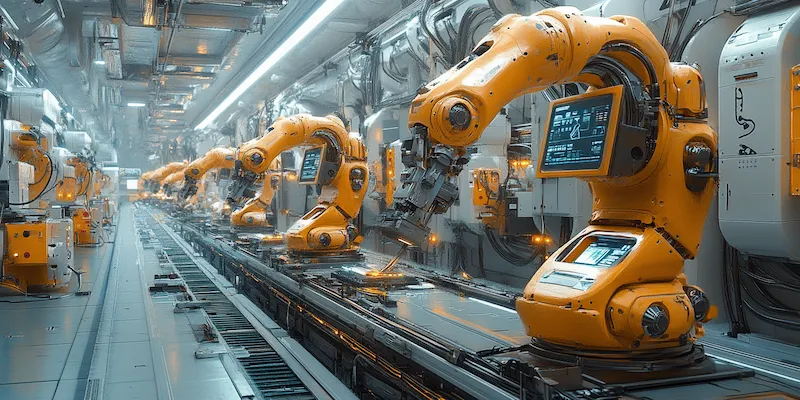
Wdrożenie zasad przemysłu 4.0 niesie ze sobą szereg korzyści dla przedsiębiorstw oraz całej gospodarki. Przede wszystkim zwiększa efektywność procesów produkcyjnych poprzez automatyzację i optymalizację działań, co prowadzi do redukcji kosztów operacyjnych. Dzięki zastosowaniu nowoczesnych technologii możliwe jest również skrócenie czasu realizacji zamówień oraz poprawa jakości produktów, co przekłada się na większą satysfakcję klientów. Przemysł 4.0 umożliwia także lepsze zarządzanie zasobami dzięki analizie danych w czasie rzeczywistym, co pozwala na szybsze reagowanie na zmiany popytu czy awarie maszyn. Inwestycje w nowe technologie mogą przyczynić się do wzrostu konkurencyjności firm na rynku krajowym i międzynarodowym.
Jakie wyzwania wiążą się z przemysłem 4.0?
Mimo licznych korzyści, wdrożenie przemysłu 4.0 wiąże się również z szeregiem wyzwań, które przedsiębiorstwa muszą pokonać. Jednym z najważniejszych problemów jest konieczność inwestycji w nowoczesne technologie oraz infrastrukturę IT, co może być kosztowne dla wielu firm, zwłaszcza tych mniejszych. Ponadto istnieje potrzeba przeszkolenia pracowników w zakresie obsługi nowych systemów oraz technologii, co wymaga czasu i zasobów ludzkich. Kolejnym wyzwaniem jest bezpieczeństwo danych i ochrona przed cyberatakami, które stają się coraz bardziej powszechne w erze cyfrowej transformacji. Firmy muszą zadbać o odpowiednie zabezpieczenia swoich systemów informatycznych oraz przestrzegać regulacji dotyczących ochrony danych osobowych.
Jakie są przykłady zastosowania przemysłu 4.0 w praktyce?
Przemysł 4.0 znajduje zastosowanie w wielu branżach, a jego implementacja przynosi wymierne korzyści. W sektorze motoryzacyjnym, na przykład, firmy takie jak BMW czy Ford wykorzystują zaawansowane systemy produkcyjne, które pozwalają na elastyczne dostosowanie linii produkcyjnych do zmieniających się potrzeb rynku. Dzięki zastosowaniu robotów współpracujących możliwe jest zwiększenie wydajności oraz poprawa jakości montażu pojazdów. W branży spożywczej, firmy takie jak Nestlé wdrażają technologie IoT do monitorowania procesów produkcyjnych, co pozwala na lepsze zarządzanie jakością oraz bezpieczeństwem żywności. Z kolei w sektorze energetycznym, przedsiębiorstwa korzystają z analizy big data do optymalizacji produkcji energii oraz przewidywania awarii w infrastrukturze.
Jakie umiejętności są potrzebne w erze przemysłu 4.0?
W obliczu dynamicznych zmian związanych z przemysłem 4.0 rośnie zapotrzebowanie na nowe umiejętności i kompetencje wśród pracowników. Kluczowe stają się umiejętności związane z technologiami informacyjnymi oraz analityką danych, ponieważ pracownicy muszą być w stanie interpretować i wykorzystywać dane generowane przez nowoczesne systemy produkcyjne. Znajomość programowania oraz obsługi robotów i automatyki również staje się coraz bardziej pożądana na rynku pracy. Ponadto, umiejętność pracy w zespole oraz komunikacji międzydziałowej jest niezbędna, aby skutecznie wdrażać innowacyjne rozwiązania i współpracować przy projektach interdyscyplinarnych.
Jakie są różnice między przemysłem 4.0 a wcześniejszymi rewolucjami przemysłowymi?
Przemysł 4.0 różni się od wcześniejszych rewolucji przemysłowych pod wieloma względami. Pierwsza rewolucja przemysłowa koncentrowała się głównie na mechanizacji produkcji za pomocą maszyn parowych, co znacznie zwiększyło wydajność pracy rąk ludzkich. Druga rewolucja przyniosła masową produkcję dzięki zastosowaniu elektryczności oraz taśm montażowych, co umożliwiło produkcję na niespotykaną wcześniej skalę. Trzecia rewolucja to era automatyzacji i komputeryzacji procesów produkcyjnych, gdzie komputery zaczęły odgrywać kluczową rolę w zarządzaniu produkcją i kontrolą jakości. Przemysł 4.0 natomiast kładzie nacisk na integrację technologii cyfrowych z fizycznymi procesami produkcyjnymi poprzez wykorzystanie Internetu rzeczy, sztucznej inteligencji i analizy danych w czasie rzeczywistym.
Jakie są perspektywy rozwoju przemysłu 4.0 w przyszłości?
Perspektywy rozwoju przemysłu 4.0 są niezwykle obiecujące, a wiele prognoz wskazuje na dalszy wzrost znaczenia technologii cyfrowych w procesach produkcyjnych. W miarę jak technologia będzie się rozwijać, można spodziewać się jeszcze większej automatyzacji procesów oraz integracji różnych systemów informacyjnych w ramach zakładów produkcyjnych. Przemiany te mogą prowadzić do powstania inteligentnych fabryk, gdzie maszyny będą mogły samodzielnie podejmować decyzje oparte na analizie danych oraz komunikować się ze sobą w celu optymalizacji procesów produkcyjnych. Dodatkowo rozwój sztucznej inteligencji może przyczynić się do powstania bardziej zaawansowanych systemów predykcyjnych, które będą w stanie przewidywać awarie czy potrzeby serwisowe maszyn jeszcze przed ich wystąpieniem.
Jakie są kluczowe trendy związane z przemysłem 4.0?
W kontekście przemysłu 4.0 można zauważyć kilka kluczowych trendów, które mają wpływ na jego rozwój i implementację w różnych branżach. Jednym z nich jest rosnąca popularność technologii chmurowych, które umożliwiają przechowywanie i przetwarzanie danych w sposób elastyczny i skalowalny. Dzięki chmurze przedsiębiorstwa mogą łatwiej integrować różne systemy informacyjne oraz uzyskiwać dostęp do danych z dowolnego miejsca na świecie. Kolejnym istotnym trendem jest rozwój sztucznej inteligencji i uczenia maszynowego, które pozwalają na automatyzację analizy danych oraz podejmowanie bardziej trafnych decyzji biznesowych opartych na dużych zbiorach informacji. Również Internet rzeczy staje się coraz bardziej powszechny, umożliwiając połączenie maszyn i urządzeń w sieci oraz monitorowanie ich stanu w czasie rzeczywistym.
Jakie są różnice między przemysłem 4.0 a tradycyjnymi metodami produkcji?
Różnice między przemysłem 4.0 a tradycyjnymi metodami produkcji są znaczące i dotyczą wielu aspektów funkcjonowania przedsiębiorstw. Tradycyjne metody produkcji często opierały się na stałych liniach montażowych oraz manualnej obsłudze maszyn przez pracowników, co ograniczało elastyczność procesów i czas reakcji na zmieniające się potrzeby rynku. W przeciwieństwie do tego, przemysł 4.0 stawia na automatyzację oraz integrację technologii cyfrowych z fizycznymi procesami produkcyjnymi, co pozwala na szybsze dostosowywanie się do zmian popytu oraz personalizację produktów zgodnie z wymaganiami klientów.
Jakie są najważniejsze wyzwania dla firm przy wdrażaniu przemysłu 4.0?
Wdrażanie zasad przemysłu 4.0 wiąże się z szeregiem wyzwań dla firm, które chcą skorzystać z nowoczesnych technologii i innowacyjnych rozwiązań w swoich procesach produkcyjnych. Jednym z kluczowych wyzwań jest konieczność inwestycji finansowych w nowoczesne technologie oraz infrastrukturę IT, co może być trudne dla mniejszych przedsiębiorstw o ograniczonych budżetach. Dodatkowo wiele firm boryka się z brakiem odpowiednich kompetencji u pracowników, co wymaga przeprowadzenia szkoleń i programów edukacyjnych dotyczących obsługi nowych systemów technologicznych oraz analizy danych. Kolejnym wyzwaniem jest kwestia bezpieczeństwa danych – przedsiębiorstwa muszą zadbać o odpowiednie zabezpieczenia przed cyberatakami oraz przestrzeganie regulacji dotyczących ochrony danych osobowych klientów i pracowników.