Destylarka do rozpuszczalników to urządzenie, które wykorzystuje proces destylacji do oddzielania różnych substancji chemicznych na podstawie ich temperatury wrzenia. Proces ten jest niezwykle istotny w wielu branżach, takich jak przemysł chemiczny, farmaceutyczny czy kosmetyczny. W destylacji najpierw podgrzewa się mieszaninę rozpuszczalników, co prowadzi do odparowania substancji o niższej temperaturze wrzenia. Para następnie przechodzi przez chłodnicę, gdzie skrapla się z powrotem w cieczy. Dzięki temu możliwe jest uzyskanie czystego rozpuszczalnika, który można ponownie wykorzystać lub przechować. Warto zaznaczyć, że różne rodzaje destylarek mogą mieć różne zastosowania i parametry techniczne, co wpływa na ich efektywność. Na przykład, w przypadku destylacji frakcyjnej można oddzielić kilka składników z mieszaniny jednocześnie, co jest szczególnie przydatne w przemyśle petrochemicznym.
Jakie są zalety korzystania z destylarki do rozpuszczalników
Korzystanie z destylarki do rozpuszczalników niesie ze sobą wiele korzyści, które mogą znacząco wpłynąć na efektywność pracy w laboratoriach oraz zakładach przemysłowych. Po pierwsze, pozwala na odzyskiwanie cennych substancji chemicznych, co przekłada się na oszczędności finansowe oraz zmniejszenie ilości odpadów. Dzięki temu procesowi można wielokrotnie wykorzystywać te same rozpuszczalniki, co jest korzystne zarówno dla budżetu firmy, jak i dla środowiska. Po drugie, destylacja umożliwia uzyskanie wysokiej czystości produktów końcowych, co jest kluczowe w wielu zastosowaniach przemysłowych i laboratoryjnych. Czystość substancji ma ogromne znaczenie w produkcji leków czy kosmetyków, gdzie nawet minimalne zanieczyszczenia mogą wpłynąć na jakość finalnego produktu.
Jakie rodzaje destylarek do rozpuszczalników są dostępne
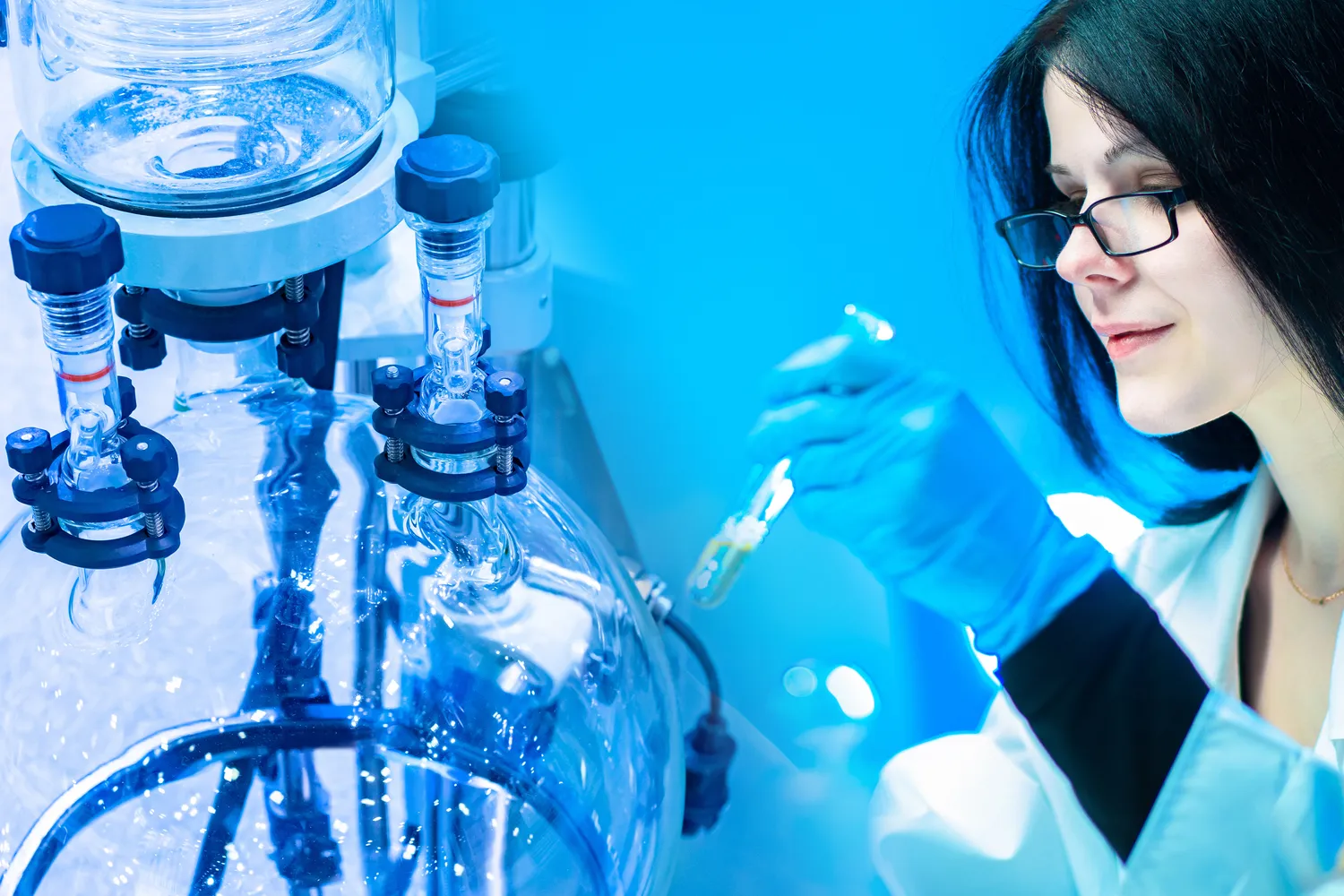
Na rynku dostępnych jest wiele różnych rodzajów destylarek do rozpuszczalników, które różnią się zarówno budową, jak i zastosowaniem. Najpopularniejsze modele to destylarki prostokątne oraz cylindryczne, które mogą być stosowane w laboratoriach oraz zakładach przemysłowych. Destylarki prostokątne charakteryzują się większą powierzchnią parowania i są często używane do dużych ilości materiału. Z kolei destylarki cylindryczne są bardziej kompaktowe i idealnie nadają się do mniejszych aplikacji. Innym rodzajem są destylarki frakcyjne, które umożliwiają separację kilku składników z mieszaniny jednocześnie dzięki zastosowaniu kolumny frakcyjnej. Warto również wspomnieć o destylarkach rotacyjnych, które działają na zasadzie obrotu naczynia z cieczą, co zwiększa efektywność procesu destylacji poprzez zwiększenie powierzchni kontaktu między parą a cieczą.
Jakie zastosowania mają destylarki do rozpuszczalników w przemyśle
Destylarki do rozpuszczalników znajdują szerokie zastosowanie w różnych gałęziach przemysłu, co czyni je niezwykle ważnym narzędziem w procesach produkcyjnych. W przemyśle chemicznym służą one do oczyszczania surowców oraz odzyskiwania cennych substancji chemicznych z odpadów produkcyjnych. Dzięki temu możliwe jest nie tylko zmniejszenie kosztów produkcji, ale także ograniczenie negatywnego wpływu na środowisko poprzez redukcję odpadów. W branży farmaceutycznej destylarki są wykorzystywane do produkcji wysokiej jakości leków oraz substancji czynnych. Czystość produktów końcowych jest kluczowa dla bezpieczeństwa pacjentów i skuteczności terapii. W przemyśle kosmetycznym natomiast destylacja pozwala na uzyskanie czystych olejków eterycznych oraz innych składników aktywnych stosowanych w kosmetykach. Oprócz tego destylarki znajdują zastosowanie w laboratoriach badawczych, gdzie służą do analizy składu chemicznego próbek oraz przygotowywania roztworów o określonych stężeniach.
Jakie czynniki wpływają na wybór destylarki do rozpuszczalników
Wybór odpowiedniej destylarki do rozpuszczalników jest kluczowy dla efektywności procesów produkcyjnych oraz jakości uzyskiwanych produktów. Istnieje wiele czynników, które należy wziąć pod uwagę przy podejmowaniu decyzji. Po pierwsze, istotne jest określenie rodzaju substancji, które będą poddawane destylacji. Różne rozpuszczalniki mają różne temperatury wrzenia, co może wpłynąć na wybór odpowiedniego modelu destylarki. Po drugie, wydajność urządzenia jest niezwykle ważna. W zależności od potrzeb produkcyjnych, można wybrać destylarki o różnej pojemności i szybkości działania. Kolejnym czynnikiem jest łatwość obsługi i konserwacji urządzenia. Nowoczesne destylarki często są wyposażone w automatyczne systemy monitorowania, co ułatwia ich użytkowanie oraz zwiększa bezpieczeństwo pracy. Dodatkowo warto zwrócić uwagę na materiały, z których wykonana jest destylarka, ponieważ mają one wpływ na trwałość oraz odporność na działanie chemikaliów.
Jakie są najczęstsze problemy związane z destylarkami do rozpuszczalników
Podczas użytkowania destylarek do rozpuszczalników mogą wystąpić różne problemy, które mogą wpłynąć na efektywność procesu destylacji oraz jakość uzyskiwanych produktów. Jednym z najczęstszych problemów jest zatykanie się kolumny destylacyjnej lub chłodnicy, co prowadzi do obniżenia wydajności urządzenia. Zatykanie może być spowodowane osadami chemicznymi lub zanieczyszczeniami obecnymi w przetwarzanym materiale. Innym problemem może być niewłaściwe ustawienie temperatury, co skutkuje niepełną separacją składników mieszaniny. Zbyt niska temperatura może prowadzić do tego, że niektóre substancje nie odparują, podczas gdy zbyt wysoka może spowodować ich degradację. Problemy z uszczelnieniami również mogą występować, co prowadzi do utraty pary i obniżenia efektywności procesu. Warto także zwrócić uwagę na regularne przeglądy i konserwację urządzenia, aby uniknąć poważniejszych awarii.
Jakie są różnice między destylacją prostą a frakcyjną
Destylacja prosta i frakcyjna to dwa podstawowe rodzaje procesów stosowanych w destylacji rozpuszczalników, które różnią się zarówno zasadą działania, jak i zastosowaniem. Destylacja prosta polega na podgrzewaniu mieszaniny cieczy do momentu jej odparowania i skraplania pary w jednym etapie. Jest to proces stosunkowo prosty i szybki, jednak ma swoje ograniczenia – najlepiej sprawdza się w przypadku mieszanin składających się z dwóch składników o znacznie różnych temperaturach wrzenia. Z kolei destylacja frakcyjna jest bardziej skomplikowanym procesem, który pozwala na oddzielanie kilku składników jednocześnie dzięki zastosowaniu kolumny frakcyjnej. W tym przypadku para przechodzi przez kolumnę, gdzie wielokrotnie skrapla się i odparowuje, co umożliwia dokładniejsze oddzielenie składników o podobnych temperaturach wrzenia. Destylacja frakcyjna jest szczególnie przydatna w przemyśle petrochemicznym oraz chemicznym, gdzie konieczne jest uzyskanie wysokiej czystości produktów końcowych.
Jakie są najlepsze praktyki przy używaniu destylarki do rozpuszczalników
Aby zapewnić efektywność i bezpieczeństwo pracy z destylarką do rozpuszczalników, warto przestrzegać kilku najlepszych praktyk. Po pierwsze, przed rozpoczęciem pracy należy dokładnie zapoznać się z instrukcją obsługi urządzenia oraz zasadami bezpieczeństwa. Ważne jest również przeprowadzenie dokładnej inspekcji sprzętu przed każdym użyciem – należy sprawdzić stan uszczelek, połączeń oraz elementów grzewczych. Po drugie, zawsze należy stosować odpowiednie środki ochrony osobistej, takie jak rękawice czy okulary ochronne, aby minimalizować ryzyko kontaktu z chemikaliami lub wysoką temperaturą. Kolejną istotną praktyką jest monitorowanie parametrów pracy destylarki podczas procesu – kontrolowanie temperatury oraz ciśnienia pozwala na szybką reakcję w przypadku wystąpienia nieprawidłowości. Dodatkowo regularne czyszczenie urządzenia po zakończeniu pracy pozwala uniknąć gromadzenia się osadów chemicznych oraz poprawia wydajność kolejnych procesów destylacyjnych.
Jakie są koszty zakupu i eksploatacji destylarki do rozpuszczalników
Koszty zakupu i eksploatacji destylarki do rozpuszczalników mogą się znacznie różnić w zależności od rodzaju urządzenia oraz jego specyfikacji technicznych. Na rynku dostępne są zarówno modele budżetowe, które mogą kosztować kilka tysięcy złotych, jak i zaawansowane systemy przemysłowe o cenach przekraczających kilkaset tysięcy złotych. Przy wyborze odpowiedniej destylarki warto uwzględnić nie tylko cenę zakupu, ale także koszty eksploatacji związane z energią elektryczną potrzebną do podgrzewania cieczy oraz ewentualnymi materiałami eksploatacyjnymi takimi jak uszczelki czy filtry. Dodatkowo warto pamiętać o kosztach serwisowania urządzenia – regularne przeglądy techniczne mogą wiązać się z dodatkowymi wydatkami, które należy uwzględnić w budżecie operacyjnym firmy.
Jakie innowacje technologiczne wpływają na rozwój destylarek do rozpuszczalników
W ostatnich latach obserwuje się dynamiczny rozwój technologii związanych z produkcją i użytkowaniem destylarek do rozpuszczalników. Innowacje te mają na celu zwiększenie efektywności procesów destylacyjnych oraz poprawę jakości uzyskiwanych produktów. Jednym z najważniejszych trendów jest automatyzacja procesów – nowoczesne destylarki często wyposażone są w zaawansowane systemy monitorowania i kontroli parametrów pracy, co pozwala na precyzyjne dostosowanie warunków procesu do specyfiki przetwarzanej mieszaniny. Dzięki temu możliwe jest osiągnięcie wyższej czystości produktów końcowych oraz zmniejszenie zużycia energii. Innym kierunkiem innowacji jest zastosowanie nowych materiałów konstrukcyjnych odpornych na działanie agresywnych substancji chemicznych oraz wysokich temperatur, co zwiększa trwałość urządzeń i zmniejsza koszty ich eksploatacji. Ponadto rozwijają się technologie związane z recyklingiem rozpuszczalników – nowoczesne systemy umożliwiają odzyskiwanie nawet najmniejszych ilości cennych substancji chemicznych z odpadów produkcyjnych.