Destylator przemysłowy to urządzenie, które odgrywa kluczową rolę w procesach separacji substancji chemicznych. Jego działanie opiera się na różnicy temperatur wrzenia poszczególnych składników mieszaniny. W praktyce, proces destylacji polega na podgrzewaniu cieczy do momentu, gdy jej składniki zaczynają parować. Para następnie jest schładzana, co prowadzi do kondensacji i zbierania czystego produktu. W przemyśle destylatory są wykorzystywane w różnych dziedzinach, takich jak produkcja alkoholu, rafinacja ropy naftowej czy wytwarzanie chemikaliów. W zależności od zastosowania, destylatory mogą mieć różne konstrukcje i rozmiary. Na przykład, w produkcji alkoholu stosuje się małe destylatory, które pozwalają na uzyskanie wysokiej jakości trunków. Z kolei w przemyśle petrochemicznym używa się dużych kolumn destylacyjnych, które mogą przetwarzać ogromne ilości surowca.
Jakie są rodzaje destylatorów przemysłowych i ich zastosowania
W przemyśle istnieje wiele rodzajów destylatorów, z których każdy ma swoje specyficzne zastosowanie oraz zalety. Najpopularniejsze typy to destylatory prostokątne, kolumnowe oraz frakcyjne. Destylatory prostokątne są najprostsze w budowie i często stosowane w małych zakładach produkcyjnych. Ich główną zaletą jest łatwość obsługi oraz niski koszt eksploatacji. Kolumnowe destylatory natomiast charakteryzują się dużą efektywnością separacji i są wykorzystywane w dużych zakładach przemysłowych, gdzie przetwarzane są znaczne ilości surowców. Frakcyjne destylatory pozwalają na oddzielanie wielu składników jednocześnie, co czyni je idealnym rozwiązaniem w przypadku skomplikowanych mieszanin chemicznych. Warto również wspomnieć o destylatorach próżniowych, które działają w obniżonym ciśnieniu, co pozwala na destylację substancji o wysokiej temperaturze wrzenia bez ryzyka ich rozkładu.
Jakie są kluczowe elementy konstrukcyjne destylatora przemysłowego
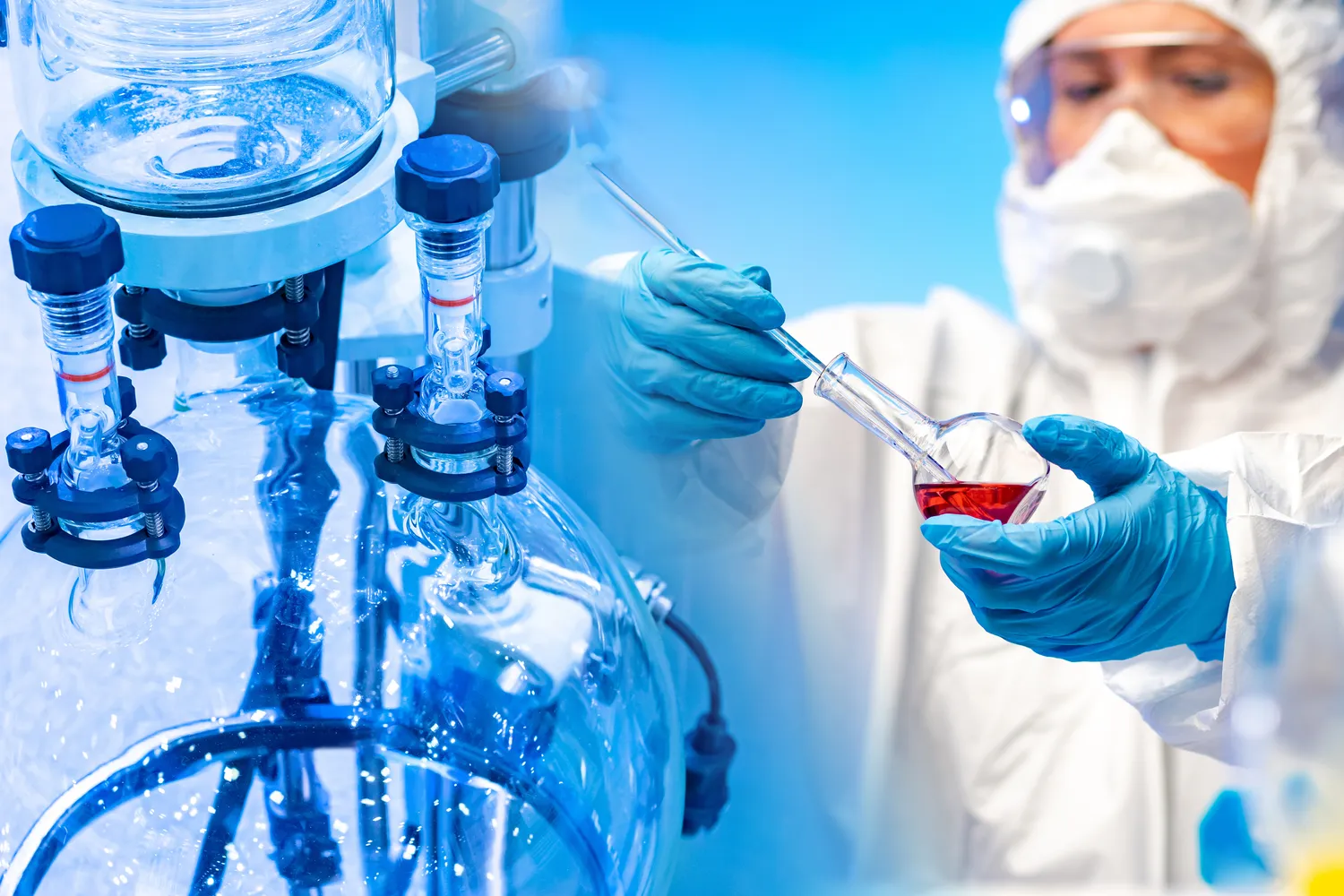
Konstrukcja destylatora przemysłowego składa się z kilku kluczowych elementów, które wpływają na jego wydajność oraz efektywność działania. Podstawowymi komponentami są zbiornik grzewczy, kolumna destylacyjna oraz kondensator. Zbiornik grzewczy służy do podgrzewania cieczy do momentu jej wrzenia. W zależności od rodzaju procesu może być wyposażony w różne źródła ciepła, takie jak palniki gazowe czy elektryczne grzałki. Kolumna destylacyjna jest miejscem, gdzie zachodzi właściwy proces separacji składników. Jej budowa może być różnorodna – od prostych konstrukcji po skomplikowane systemy z wieloma poziomami frakcjonowania. Kondensator natomiast odpowiada za schładzanie pary i jej kondensację do postaci cieczy. Oprócz tych podstawowych elementów, nowoczesne destylatory często wyposażone są w dodatkowe systemy monitorujące i kontrolujące proces, co zwiększa ich efektywność oraz bezpieczeństwo pracy.
Jakie są najważniejsze korzyści z używania destylatorów przemysłowych
Użycie destylatorów przemysłowych przynosi szereg korzyści zarówno dla producentów, jak i dla konsumentów końcowych. Przede wszystkim umożliwiają one efektywną separację składników chemicznych, co przekłada się na wyższą jakość produktów końcowych. Dzięki precyzyjnemu procesowi destylacji można uzyskać czyste substancje o wysokim stopniu koncentracji, co jest szczególnie istotne w branży farmaceutycznej czy spożywczej. Kolejną zaletą jest możliwość przetwarzania dużych ilości surowców w krótkim czasie, co znacząco zwiększa wydajność produkcji. Destylatory pozwalają także na oszczędność energii dzięki zastosowaniu nowoczesnych technologii grzewczych oraz systemów recyklingu pary wodnej. Dodatkowo wiele nowoczesnych urządzeń jest wyposażonych w funkcje automatyzacji procesów, co redukuje potrzebę zatrudniania dużej liczby pracowników oraz minimalizuje ryzyko błędów ludzkich.
Jakie są najczęstsze problemy z destylatorami przemysłowymi
Podczas eksploatacji destylatorów przemysłowych mogą wystąpić różne problemy, które wpływają na ich wydajność oraz jakość uzyskiwanych produktów. Jednym z najczęstszych kłopotów jest osadzanie się zanieczyszczeń w kolumnie destylacyjnej, co prowadzi do obniżenia efektywności separacji. Zanieczyszczenia te mogą pochodzić z surowców, które są przetwarzane, lub być wynikiem reakcji chemicznych zachodzących w trakcie destylacji. Regularne czyszczenie kolumny oraz monitorowanie jakości surowców to kluczowe działania, które mogą pomóc w uniknięciu tego problemu. Innym istotnym zagadnieniem jest kontrola temperatury w procesie destylacji. Niewłaściwe ustawienie temperatury może prowadzić do niepełnej separacji składników, co skutkuje obniżoną jakością produktu końcowego. Warto również zwrócić uwagę na systemy chłodzenia, które mogą ulegać awariom, co prowadzi do nieefektywnego kondensowania pary.
Jakie są nowoczesne technologie w destylacji przemysłowej
W ostatnich latach nastąpił znaczny postęp technologiczny w dziedzinie destylacji przemysłowej, co przyczyniło się do zwiększenia efektywności i bezpieczeństwa procesów produkcyjnych. Nowoczesne destylatory często wyposażone są w zaawansowane systemy automatyzacji, które umożliwiają precyzyjne monitorowanie i kontrolowanie parametrów pracy urządzenia. Dzięki zastosowaniu czujników temperatury, ciśnienia oraz przepływu możliwe jest bieżące dostosowywanie warunków pracy destylatora, co przekłada się na lepszą jakość uzyskiwanych produktów oraz oszczędność energii. Kolejnym innowacyjnym rozwiązaniem są destylatory oparte na technologii membranowej, które pozwalają na separację składników bez konieczności podgrzewania cieczy. Tego rodzaju urządzenia charakteryzują się niskim zużyciem energii oraz minimalnym wpływem na środowisko. Warto również wspomnieć o zastosowaniu sztucznej inteligencji i algorytmów uczenia maszynowego w optymalizacji procesów destylacyjnych.
Jakie są koszty związane z zakupem i eksploatacją destylatora przemysłowego
Koszty związane z zakupem i eksploatacją destylatora przemysłowego mogą być znaczące i różnią się w zależności od wielu czynników, takich jak typ urządzenia, jego wydajność oraz dodatkowe funkcje. Na początku należy uwzględnić koszt zakupu samego destylatora, który może wynosić od kilku tysięcy do nawet milionów złotych w przypadku dużych kolumn destylacyjnych. Oprócz samego zakupu należy także brać pod uwagę koszty instalacji oraz uruchomienia urządzenia, które mogą wymagać specjalistycznych prac budowlanych oraz elektrycznych. Kolejnym istotnym elementem kosztowym są wydatki związane z eksploatacją, takie jak zużycie energii elektrycznej czy paliwa wykorzystywanego do podgrzewania cieczy. Warto również pamiętać o kosztach konserwacji i serwisowania urządzenia, które powinny być regularnie przeprowadzane w celu zapewnienia jego długotrwałej wydajności. Dodatkowo należy uwzględnić koszty związane z zatrudnieniem personelu obsługującego destylator oraz ewentualne szkolenia dla pracowników.
Jakie są regulacje prawne dotyczące użycia destylatorów przemysłowych
Użycie destylatorów przemysłowych wiąże się z przestrzeganiem różnych regulacji prawnych, które mają na celu zapewnienie bezpieczeństwa pracy oraz ochrony środowiska. W wielu krajach istnieją przepisy dotyczące produkcji alkoholu, które wymagają uzyskania odpowiednich zezwoleń na prowadzenie działalności związanej z destylacją. Przepisy te regulują m.in. kwestie związane z jakością surowców, procesem produkcji oraz kontrolą jakości końcowego produktu. W przypadku przemysłu chemicznego istotne są normy dotyczące emisji substancji szkodliwych do atmosfery oraz zarządzania odpadami powstającymi podczas procesu destylacji. Firmy zajmujące się produkcją muszą również przestrzegać przepisów BHP, które określają zasady bezpieczeństwa pracy przy obsłudze urządzeń destylacyjnych.
Jakie są przyszłe kierunki rozwoju technologii destylacyjnej
Przyszłość technologii destylacyjnej zapowiada się obiecująco dzięki ciągłemu rozwojowi innowacyjnych rozwiązań oraz rosnącemu naciskowi na efektywność energetyczną i ochronę środowiska. Jednym z głównych kierunków rozwoju jest dalsza automatyzacja procesów produkcyjnych poprzez zastosowanie sztucznej inteligencji i analizy danych. Dzięki tym technologiom możliwe będzie jeszcze bardziej precyzyjne monitorowanie parametrów pracy urządzeń oraz optymalizacja procesów w czasie rzeczywistym. Kolejnym ważnym trendem jest rozwój technologii membranowej oraz innych alternatywnych metod separacji substancji chemicznych, które mogą zastąpić tradycyjne metody destylacyjne w niektórych zastosowaniach. Takie rozwiązania charakteryzują się mniejszym zużyciem energii oraz niższym wpływem na środowisko naturalne. Również coraz większą uwagę przykłada się do kwestii recyklingu materiałów i minimalizacji odpadów powstających podczas procesu produkcji.
Jak wybrać odpowiedni destylator przemysłowy dla swojej firmy
Wybór odpowiedniego destylatora przemysłowego dla firmy to kluczowy krok, który może wpłynąć na efektywność produkcji oraz jakość końcowych produktów. Przed podjęciem decyzji warto dokładnie przeanalizować potrzeby swojej firmy oraz specyfikę procesów produkcyjnych. Na początku należy określić rodzaj surowców, które będą przetwarzane oraz ich właściwości fizykochemiczne, ponieważ różne substancje wymagają różnych podejść do procesu destylacji. Następnie warto zwrócić uwagę na wydajność urządzenia – im większa wydajność, tym więcej surowca można przetworzyć w krótszym czasie. Kolejnym aspektem jest konstrukcja i rodzaj destylatora – wybór między prostokątnymi a kolumnowymi modelami powinien być uzależniony od specyfiki produkcji oraz wymagań jakościowych końcowego produktu. Nie można zapominać o kosztach eksploatacji – warto porównać różne modele pod kątem zużycia energii oraz kosztów konserwacji.